精密铸造
精密铸造工艺过程质量控制,确保铸件质量和工艺稳定性
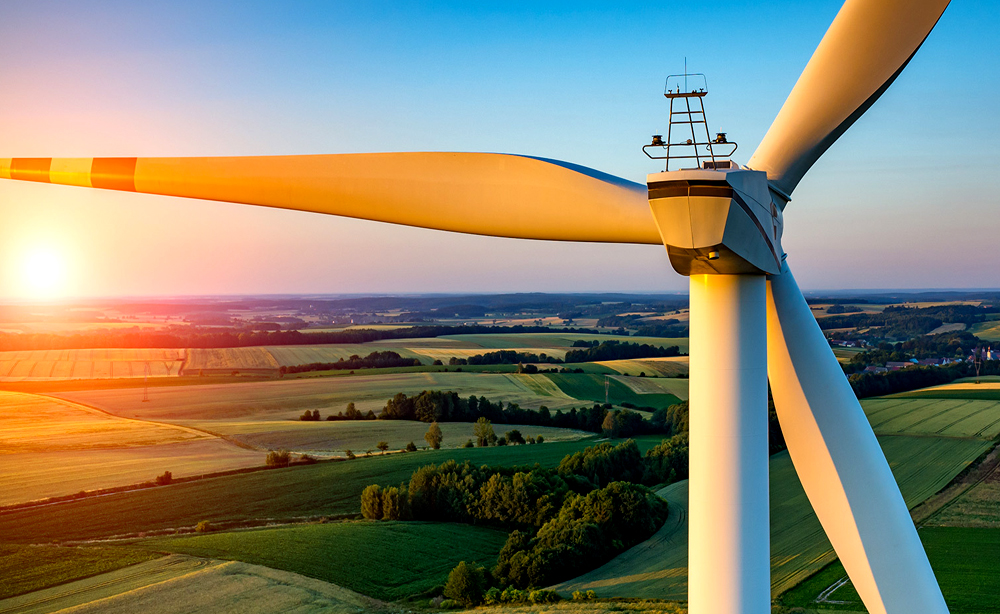
应用场景
铸件质量检测
铸件内部气孔、夹杂、裂纹等缺陷检测
模具检测
铸造模具型腔质量和使用状态检测
熔炼监测
熔炼炉内部状态和熔炼过程监测
工艺优化
铸造工艺参数优化和质量改进
精密铸造应用领域
领域概述
精密铸造是现代制造业的重要工艺,广泛应用于航空航天、汽车、机械、电力等行业。铸件质量直接影响最终产品的性能和可靠性,因此对铸造过程的质量控制要求极高。
工业内窥镜技术为精密铸造提供了强有力的质量检测手段,能够深入铸件内部,检测各种缺陷,监控工艺过程,为铸造质量控制和工艺优化提供科学依据。
主要应用场景
铸件内部缺陷检测
铸件在凝固过程中容易产生气孔、夹杂、缩孔、裂纹等内部缺陷,这些缺陷会严重影响铸件的力学性能和使用寿命。通过工业内窥镜技术,可以对铸件内部进行全面检测,及时发现和评估各种缺陷。
检测内容:
- 气孔大小和分布检测
- 夹杂物类型和位置识别
- 缩孔缩松程度评估
- 裂纹长度和深度测量
铸造模具检测
模具是铸造生产的关键工装,其质量直接影响铸件质量和生产效率。内窥镜技术能够对模具型腔进行详细检测,确保模具质量和延长使用寿命。
检测项目:
- 型腔表面质量检测
- 分型面配合精度检查
- 浇注系统通畅性检测
- 冷却系统状态监测
熔炼过程监测
熔炼是铸造工艺的重要环节,熔炼质量直接影响铸件质量。通过耐高温内窥镜技术,可以对熔炼炉内部状态进行实时监测,优化熔炼工艺。
监测内容:
- 炉衬磨损状态检测
- 熔体流动状态观察
- 炉内温度分布监测
- 渣层厚度测量
铸造工艺优化
基于内窥镜检测数据,可以对铸造工艺参数进行优化,提高铸件质量和生产效率。
优化方向:
- 浇注系统设计优化
- 冷却速度控制优化
- 模具温度分布优化
- 脱模工艺改进
技术优势
高温适应性
专门开发的耐高温探头技术,能够在铸造高温环境下正常工作,满足熔炼和浇注过程的监测需求。
缺陷识别精度
采用先进的图像处理算法和人工智能技术,能够准确识别和分类各种铸造缺陷,提高检测精度。
3D重建技术
通过3D重建技术,能够生成铸件内部的三维模型,为缺陷定位和评估提供直观的视觉支持。
实时监测能力
支持实时监测和数据记录,能够跟踪铸造过程的动态变化,为工艺控制提供及时反馈。
铸造工艺检测
砂型铸造
- 砂型紧实度检测
- 型腔尺寸精度检查
- 浇注系统设计验证
- 铸件脱砂质量检测
精密铸造
- 蜡模质量检测
- 型壳强度检查
- 脱蜡过程监测
- 精铸件表面质量检测
压力铸造
- 压铸模具检测
- 压射过程监测
- 铸件内部质量检查
- 脱模效果评估
离心铸造
- 离心机状态检测
- 铸型质量检查
- 离心过程监测
- 铸件壁厚均匀性检测
质量标准
我们的检测服务严格遵循铸造行业质量标准:
- GB/T铸造行业国家标准
- JB/T机械行业铸造标准
- ASTM美国材料试验协会标准
- ISO国际铸造质量标准
缺陷分析
气孔缺陷
- 析出性气孔检测
- 侵入性气孔识别
- 气孔形成原因分析
- 防止措施建议
夹杂缺陷
- 金属夹杂物检测
- 非金属夹杂物识别
- 夹杂来源分析
- 净化措施优化
裂纹缺陷
- 热裂纹检测
- 冷裂纹识别
- 裂纹扩展评估
- 预防措施制定
缩孔缩松
- 缩孔位置定位
- 缩松程度评估
- 补缩效果检查
- 工艺改进建议
行业应用
航空铸件
- 发动机叶片铸造检测
- 机匣类铸件质量控制
- 精密结构件检测
- 特种合金铸造监测
汽车铸件
- 发动机缸体检测
- 变速箱壳体检测
- 制动系统铸件检测
- 悬挂系统铸件检测
机械铸件
- 泵体阀体检测
- 机床床身检测
- 减速器壳体检测
- 液压件铸造检测
电力铸件
- 发电机组铸件检测
- 变压器铸件检测
- 开关设备铸件检测
- 输电设备铸件检测
服务价值
质量保证
通过全面检测,确保铸件质量符合技术要求,提高产品可靠性。
成本控制
及早发现质量问题,减少废品和返工,降低生产成本。
工艺改进
基于检测数据分析,持续改进铸造工艺,提高生产效率。
技术提升
通过专业服务,帮助客户提升铸造技术水平和管理能力。
客户案例
我们已为众多铸造企业提供专业检测服务:
- 大型铸造集团
- 汽车零部件铸造厂
- 航空铸造企业
- 机械铸造公司
通过我们的服务,客户实现了:
- 铸件合格率提升至98%以上
- 生产成本降低20%
- 工艺稳定性显著提高
- 客户满意度大幅提升