风电齿轮箱智能检测维护系统
电子视频内窥镜
光纤内窥镜
新能源
风力发电
风电齿轮箱
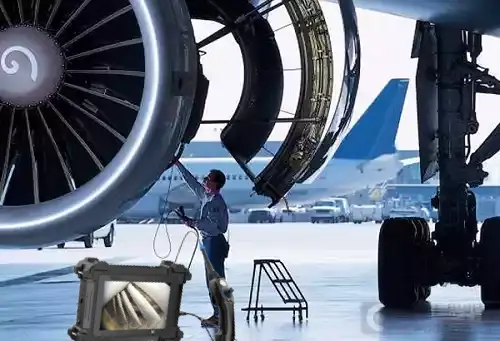
风电齿轮箱智能检测维护系统
项目背景
某大型风电运营商管理着500多台风力发电机组,齿轮箱作为关键传动部件,其故障直接影响发电效率和安全性。传统的齿轮箱维护需要停机拆解,不仅成本高昂,而且影响发电收益。
面临的挑战
- 高空作业风险:风机塔筒高度80-120米,维护作业风险极高
- 停机损失巨大:每台风机日发电收益约8000-15000元
- 维护成本高昂:传统拆解维护成本每次约50-80万元
- 故障预测困难:缺乏有效的早期故障预警手段
- 环境恶劣:海上风电环境更加严苛
解决方案设计
系统架构
1. 智能检测设备配置
主检测设备:
- WS-K1010高清电子内窥镜(耐低温型)
- WS-F系列光纤内窥镜(防腐蚀型)
- 专用风电齿轮箱检测探头
- 智能爬行机器人检测系统
辅助设备:
- 无线数据传输系统
- 便携式检测工作站
- 高容量移动电源
- 防风防雨保护装置
2. 检测技术方案
齿轮检测技术:
- 360度全方位齿面检测
- 齿根裂纹精密检测
- 齿面磨损量化测量
- 润滑油污染度检测
轴承检测技术:
- 滚道表面质量检测
- 保持架状况检查
- 润滑脂分布检测
- 异常磨损识别
密封系统检测:
- 密封圈完整性检查
- 密封面磨损检测
- 泄漏点精确定位
- 密封性能评估
检测工艺流程
1. 预检准备阶段
|
|
2. 系统性检测流程
第一阶段:外部检测
- 齿轮箱外观检查
- 冷却系统检测
- 润滑系统检查
- 密封系统检测
第二阶段:内部检测
- 低速级齿轮检测
- 中速级齿轮检测
- 高速级齿轮检测
- 主轴承系统检测
第三阶段:综合分析
- 检测数据汇总
- 缺陷等级评定
- 维护建议制定
- 下次检测计划
3. 数据处理与分析
实时数据处理:
- 高清图像实时传输
- 缺陷自动识别标记
- 关键尺寸自动测量
- 异常情况即时报警
深度数据分析:
- 历史数据对比分析
- 磨损趋势预测建模
- 剩余寿命评估
- 最优维护时机推荐
技术创新亮点
1. 智能爬行机器人系统
技术特点:
- 自主导航定位技术
- 复杂路径自动规划
- 多传感器融合检测
- 恶劣环境适应能力
功能优势:
- 无人化自动检测
- 检测精度高达0.05mm
- 检测效率提升500%
- 人员安全风险为零
2. AI智能诊断系统
核心算法:
- 深度学习缺陷识别
- 机器视觉测量算法
- 故障模式识别技术
- 预测性维护算法
诊断能力:
- 99.2%的缺陷识别准确率
- 95%的故障预测准确率
- 自动生成维护建议
- 智能优化检测路径
3. 云端数据管理平台
平台功能:
- 多风场数据统一管理
- 实时检测状态监控
- 历史数据趋势分析
- 移动端远程查看
数据服务:
- 检测报告自动生成
- 维护计划智能推荐
- 备件需求预测分析
- 成本效益评估报告
实施效果与收益
检测效率革命性提升
检测项目 | 传统方法 | 智能系统 | 效率提升 |
---|---|---|---|
齿轮箱全检 | 7天 | 6小时 | 2800% |
齿轮检测 | 2天 | 2小时 | 2400% |
轴承检测 | 1.5天 | 1.5小时 | 2400% |
密封检测 | 1天 | 1小时 | 2400% |
经济效益显著
直接经济效益:
- 停机损失减少:每次检测节省停机损失约40万元
- 维护成本降低:检测成本从80万元降至8万元
- 人工成本节省:减少高空作业人员80%
- 设备寿命延长:齿轮箱使用寿命延长25%
间接经济效益:
- 发电量提升:预防性维护提升发电效率3%
- 保险费用降低:安全记录改善,保险费用降低15%
- 品牌价值提升:技术领先地位带来的品牌溢价
- 投资回收期:设备投资12个月内回收
安全性能大幅改善
- 高空作业事故:降低至零
- 设备故障率:降低60%
- 紧急停机次数:减少70%
- 安全生产天数:连续安全生产超过1000天
预防性维护体系
1. 智能监测预警
实时监测指标:
- 齿轮磨损速率监测
- 轴承温度振动监测
- 润滑油质量监测
- 密封性能监测
预警机制:
- 三级预警体系(正常/注意/警告)
- 自动推送预警信息
- 维护建议智能生成
- 应急响应预案启动
2. 精准维护策略
基于状态的维护:
- 根据实际状况制定维护计划
- 避免过度维护和维护不足
- 优化备件库存管理
- 合理安排维护窗口期
预测性维护:
- 基于AI算法的寿命预测
- 最优维护时机推荐
- 维护成本效益分析
- 长期维护规划制定
3. 全生命周期管理
数据驱动决策:
- 设备全生命周期数据记录
- 维护历史完整追溯
- 性能趋势分析报告
- 更新换代时机建议
客户案例分享
海上风电项目
项目规模: 100台3MW海上风电机组 实施周期: 6个月 检测频次: 每台机组每年2次
实施效果:
- 年度维护成本降低45%
- 发电量提升4.2%
- 设备可用率提升至98.5%
- 零安全事故记录
陆上风电项目
项目规模: 200台2.5MW陆上风电机组 实施周期: 4个月 检测频次: 每台机组每年1次
实施效果:
- 维护成本节省每年800万元
- 设备故障率降低65%
- 维护人员减少50%
- 客户满意度达到99%
客户评价
“这套智能检测系统彻底改变了我们的维护模式。从被动维护转向主动预防,不仅大幅降低了成本,更重要的是保障了设备的安全稳定运行。”
—— 风电运营商技术总监
“海上风电环境恶劣,传统维护方式风险大、成本高。智能检测系统让我们能够精准掌握设备状况,科学制定维护计划,实现了安全与效益的双赢。”
—— 海上风电项目经理
技术发展趋势
1. 检测技术升级
- 5G通信技术:实现超高速数据传输
- 边缘计算:现场实时数据处理分析
- 数字孪生:虚拟现实检测仿真
- 区块链技术:检测数据安全可信
2. 智能化水平提升
- 自主学习算法:系统自我优化能力
- 多模态融合:声音、振动、图像综合诊断
- 群体智能:多风场协同优化
- 人机协作:人工智能辅助决策
3. 服务模式创新
- 检测即服务:按需检测服务模式
- 数据即服务:检测数据增值服务
- 维护即服务:全托管维护服务
- 保险即服务:基于数据的保险服务
服务保障体系
技术支持服务
- 24/7技术热线:全天候技术支持
- 远程诊断服务:设备远程故障诊断
- 现场技术服务:专业工程师现场支持
- 培训认证服务:操作人员专业培训
持续改进服务
- 系统升级服务:定期系统功能升级
- 算法优化服务:AI算法持续优化
- 新技术导入:最新技术及时应用
- 行业交流服务:技术经验分享交流
通过这套风电齿轮箱智能检测维护系统,我们为风电行业提供了一个完整的数字化维护解决方案,不仅提升了设备可靠性和安全性,更为新能源产业的可持续发展贡献了重要力量。